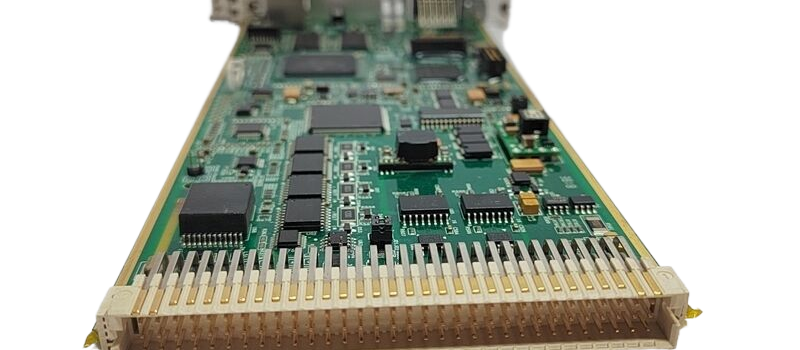
虽然典型的分布式控制系统(DCS)密切关注生产和调度,但DCS忽略了其他一些重要细节。明确地说,DCS消耗过程数据是为了测量和调节通过工厂的物料流量。它解释传感器数据并协调对最终控制元件的调整,以保持设定值。通过这种方式,输入被系统地转化为输出。
分拨中心的作用在一定程度上局限于管理物流。更具体地说,它没有考虑到工厂生产方式的健康变化。隐藏在过程数据中的是与阀门和阻尼器、PID控制器甚至物理过程本身(如最终影响生产的储罐、熔炉和热交换器)相关的重要细节。他们的健康状况直接影响生产能力、质量和能源消耗。正是这些和其他有价值的见解可以从工厂的监管控制系统中获得。
考虑工厂过程数据中容易获得的一些不同见解,所有这些都是为了提问:
肮脏的小秘密
工程师们经常将静摩擦列为阻碍高效生产的主要机械问题。事实上,当阀门被指示调节时是打开还是关闭–由于静摩擦力过大,这就成了一个问题。过度静摩擦的结果是无法精确跟踪设定点的过程。虽然完善的指标可以提供必要的信息,但静态阻力的识别和量化都不在传统DCS的范围内。
揭露不良行为
当全自动过程转换为手动模式时,常见的下意识反应是责怪负责的操作员。然而,经验告诉我们,大多数操作员将控制回路从其指定模式(例如自动、级联等)中取出。)因为不稳定的性能和对安全的担忧。这种行动应促使考虑过程的控制策略和设计,而不是操作员的责任。虽然不包括在DCS的指标中,但跟踪其“正常”模式下花费的时间循环的简单KPI提供了对该问题可能性的充分见解,并且它可以帮助流程工程师确定需要考虑的流程。
高阶问题
如果广告商的话可信,那么制造商应该投资新的优化技术,而不是调整现有系统。正如大多数从业者所知,控制器调整需要与日常输出变化相同的数据——控制器输出的变化驱动过程变量的响应。在全厂基础上模拟输出变化可以消除执行冲击测试的需要。更重要的是,这些发现可以用来隔离那些可以从调整调谐系数中受益最大的循环。这相当于实时全厂优化。
跨单位比较
DCS触发的警报通常代表症状而非根本原因。考虑一个适度的上游性能偏差,该偏差会过滤下游并影响需要控制在更严格公差范围内的流程。由此产生的对下游流程的警告可能会误导员工解决问题的真正根源。需要知道的重要一点是,与警报相关的过程数据包含有价值的线索——基于频率的指纹,可以向上游追溯并与根本原因相匹配。不幸的是,标准DCS不包括从可用过程数据中提取此类见解所需的取证工具。
从工厂监管控制数据分析中获得的一系列见解不仅限于这几个例子,还包括其他例子,如类似单元操作的比较、过程本身的健康状况等。虽然DCS和其他监督层技术被视为控制的顶点,但记住它们是建立在监管控制系统的基础上是健康的。